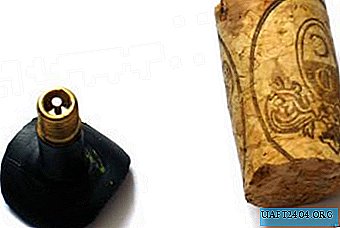



The main unit in the rocket will be a valve; the effectiveness of our entire rocket will depend on it. With it, air is forced into the bottle and held in place. Take a punctured or working chamber from any bicycle and cut out its “nipple”, the part to which we connect the pump. We also need the usual cork from bottles of wine or champagne, but since there are so many different shapes and sizes, the main selection criterion for us there will be a length of at least 30 mm and a diameter so that the cork enters the neck of the bottle with an interference fit of 2/3 of its length. Now, in the found cork, make a hole of such a diameter so that the “nipple” enters with force into it. It is better to drill a hole in two steps, first with a thin drill, and then with a drill of the desired diameter and most importantly do it gently with little effort. Then we connect the “nipple” and the cork together, after dropping a little “super glue” into the cork hole to prevent air from seeping out of the bottle. The last part in the valve will be the platform, which serves to attach the valve to the launch pad. It must be made of durable material, for example metal or fiberglass with a thickness of 2-3 mm and a size of 100x20 mm. After you have made 3 holes for the mount and nipples in it, you can glue the cork to it, while it is better to use epoxy glue for a more durable connection. As a result, the main thing is that part of the nipple protrudes above the platform by about 8-11 mm, otherwise there will be nothing to connect the pump to.
Proceeded to the rocket itself. She for its manufacture will need two bottles of 1.5 liters, a ball from table tennis, colored tape. One bottle can be set aside for now, and with the second we perform the operation. Carefully cut off the top of the bottle so that the total length is approximately 100 mm. Next, saw off the threaded head from this part. As a result, we got a head fairing, but that's not all. Since there is a hole in the middle, it needs to be closed and in this case a prepared ball will be needed. Take a whole bottle, turn it upside down, put a ball on top and put on a head fairing. In total, it turned out that the ball protrudes slightly beyond the circumference of the bottle, it will serve as an element that softens the blow to the ground when descending from orbit. Now you need to decorate the rockets a little, since the bottles are transparent, then in flight the rocket will be poorly visible and for this, where there is a smooth cylindrical surface, we wrap it with colored tape. So the cherished rocket turned out in the end, although it looks more like a ballistic intercontinental missile. You can of course make stabilizers to resemble a standard rocket, but they will not affect the flight in any way on this shell. The stabilizers in the amount of four pieces are easy to make from cardboard from under household appliances, cutting them out small in area. You can glue them to the rocket body using glue liquid nails or other similar.
Now let's start making the launch pad. To do this, we need an even plywood sheet with a thickness of 5-7 mm cut out by a square with sides 250 mm long. In the center, first we fix the previously made platform with the valve, choose the distance between the holes arbitrarily, the distance between the two platforms should be at least 60 mm and for this we use bolts with a diameter of 4 or 5 mm and a length of at least 80 mm as fasteners. Further, in order to fix the rocket on the launch pad, you will need to make a holder with a launching device, which consists of two corners, two nails and 4 bolts with fastening. At the corner on one side, we drill two holes for fasteners to the launch pad, the distance between the holes, as in the corner, and in the main platform should be the same, for example 30 mm. On the other side of both corners, you also need to make two holes with a diameter of 5 mm for two large nails of the same diameter, but the distance between the holes should be such that the distance between the nails themselves is from 28 to 30 mm. When everything is assembled, the height of the position of the fixing nails should be adjusted. To do this, install the bottle on the valve, as in combat mode, with great effort, and after that you need to choose the height of the corners so that the nails easily slide in the holes themselves and between the neck of the bottle. Nails also serve as a descent mechanism, but you still need to make a special plate connecting them for the rope, which we will pull to launch the rocket. The final element in the launch pad will be the legs, for which you need to drill 4 holes in all corners of the pad and fasten 4 small bolts with a length of 30 to 50 mm, they serve to fix the launch pad in the ground.
The rocket must be filled with water in a strictly specified amount, this is 1/3 of the total length of the entire bottle. It is easy to make sure by experience that it’s not worth filling in too much water, as well as too little, since in the first case there is too little space for air, and in the second too much. The engine thrust in these cases will be very weak, and the operating time will be short. When the valve opens, compressed air begins to eject water through the nozzle, resulting in thrust, and the rocket develops an appropriate speed (about 12 m / s). It should be borne in mind that the cross-sectional area of the nozzle also affects the thrust. The thrust that decreases as water is thrown out will allow the rocket to reach a height of 30-50 m.
Several test launches in light or moderate winds allow us to conclude that with a tight connection between the valve and the bottle, proper filling with water and vertical installation of the model at the start, it can reach a height of about 50 m. Setting the rocket at an angle of 60 ° leads to a decrease in height lift, however, the flight range increases. With more gentle paths, either the model starts will fail, or the flight range will be small. A model launched without water will be very light and will rise only 2 - 5 m. Launches of air-hydraulic models are best done in calm weather. As a result of the tests, it is easy to notice that the model has good stability and a tendency to orient itself against the wind, both in the presence of traction and after the end of engine operation. The flight time of the model from start to landing, depending on the altitude reached, is 5 - 7 seconds.
By the way, air-hydraulic missiles can also be multi-stage, that is, consist of several bottles or even five or more. In general, a record for the flight altitude of such a rocket is as much as 600 meters, not every standard model of a rocket can reach such a height. At the same time, they can raise a significant payload, for example, some testers install cameras or mini video cameras and successfully carry out aerial photography.
So, when everything is ready, you can go out and make the first launches. Together with the rocket and equipment, you still need to take additional fuel - a few bottles of water. Such missiles can be launched anywhere, in the schoolyard, in a forest clearing, the main thing is that within a radius of 20 meters there should not be any buildings that impede combat flight. At the center of our training ground, set the launch pad so that the mounted rocket is strictly vertical. Next, we connect the pump to the valve, fill the rocket with the water of the prescribed volume and quickly install it on the launch pad, so that the valve fits very tightly into the neck of the bottle. Now cock the trigger, insert two nails into the holes, fixing them. It’s better to launch an air-hydraulic rocket together, one will pull the rope - start, and the other to pump air into the bottle. The length of the rope should be about 10 - 15 meters, this distance is enough to prevent the launching person from spraying fountain water from the rocket, but you will not envy anyone who will operate the pump, he has very good chances to take a cool shower with an unusual flight of a rocket. Since our rocket consists of a bottle with a volume of 1.5 liters, it should be inflated to a pressure of 4 to 5 atmospheres, you can try more, but the valve itself and the connection to the pump will not withstand such a high pressure, and there will be a leak. When pumping, you can not be afraid that something can happen to the bottle, because it can withstand 30 to 40 atmospheres according to technical data. Air injection lasts approximately 30 seconds. When the desired pressure in the bottle is reached, the launch team is given the “Start” command, which pulls the rope with a sharp movement and after a moment the rocket rushes into the sky, performing a combat mission. rocket trajectory. For the next launch, it remains only to fill the fuel from the reserve and again pump air into the engine compartment. Such a rocket can well entertain on a summer sunny day.